Custom Damascus Folding Knives: The Ultimate Guide
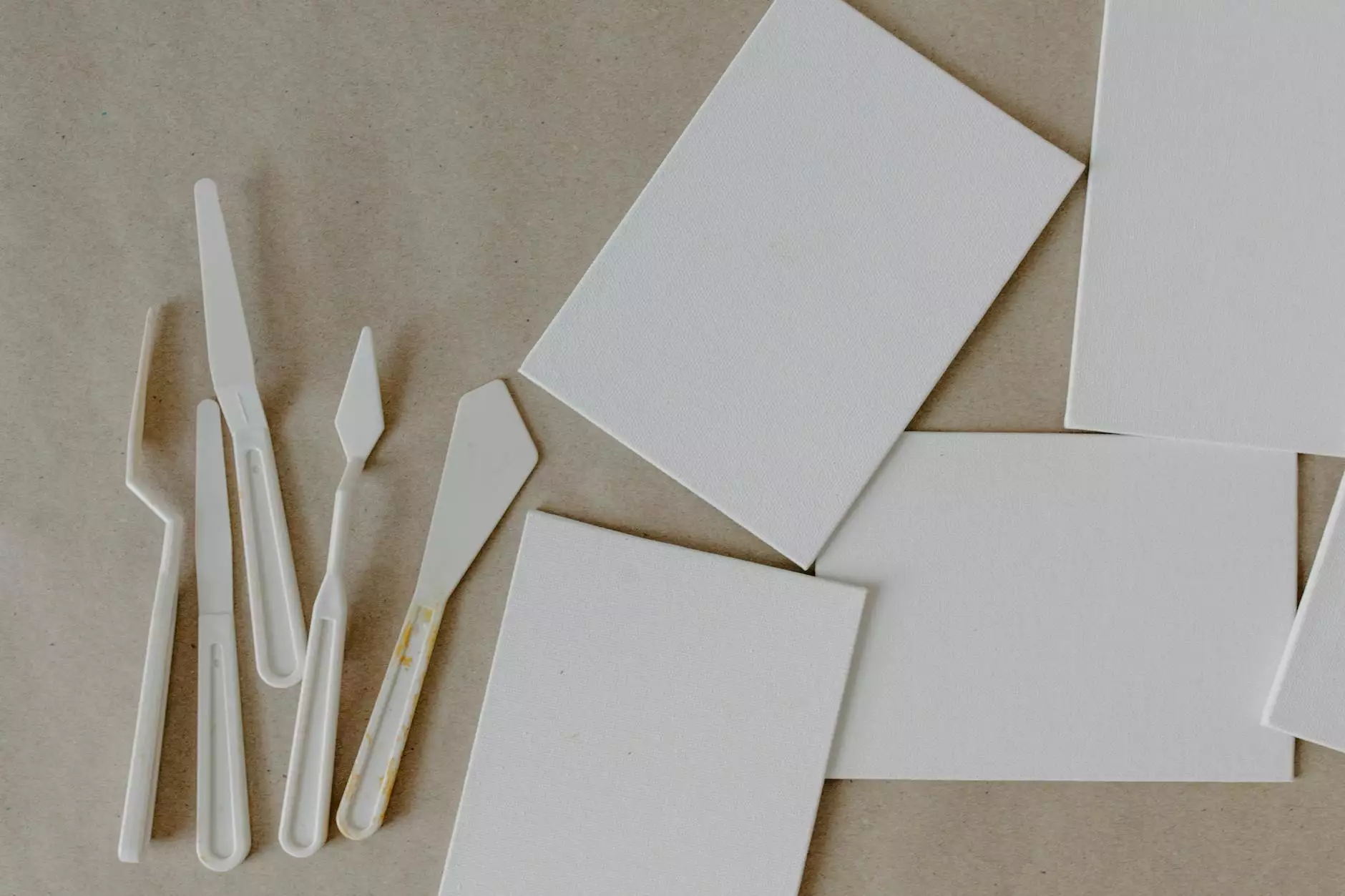
When it comes to custom damascus folding knives, enthusiasts and collectors alike treasure the beauty, strength, and functionality that these knives offer. This article will delve into the intricate world of custom damascus folding knives, exploring their rich history, unique manufacturing processes, and practical applications. Whether you’re an outdoor adventurer or a knife collector, understanding these remarkable tools is essential to appreciate their value fully.
What Are Custom Damascus Folding Knives?
Custom damascus folding knives are made from a type of steel known for its distinctive patterns and exceptional resilience. The process of creating damascus steel involves layering different types of steel and forging them together. The result is a blade that not only performs exceptionally well but is also visually stunning.
History of Damascus Steel
The history of damascus steel dates back to ancient times, where it was originally used for making swords and other weapons. Named after the city of Damascus, where it was prominently traded, the steel was known for its superior strength and ability to hold a sharp edge. Over centuries, the craft has evolved, leading to modern techniques that still capture the essence of this time-honored tradition.
The Craftsmanship Behind Custom Damascus Folding Knives
Creating a custom damascus folding knife involves meticulous craftsmanship. Here are the key steps in the process:
1. Selecting Materials
High-quality steel is essential for a durable and efficient folding knife. Manufacturers typically use a combination of high-carbon steel and stainless steel to achieve the desired properties.
2. Forging the Steel
The forging process is where the magic happens. Layers of steel are forge-welded together at high temperatures. This process not only combines the elements but also creates the beautiful patterns that are characteristic of damascus steel.
3. Shaping the Blade
Once the steel is forged, the craftsman shapes the blade. This step requires skill and precision to ensure the knife not only looks good but also functions perfectly. The blade is then ground to achieve the desired sharpness.
4. Heat Treatment
Heat treatment is crucial for enhancing the blade's durability and edge retention. It involves heating the blade to a specific temperature and then cooling it rapidly to achieve the right molecular structure.
5. Handle and Lock Mechanism
The handle of a folding knife can be made from various materials, such as wood, micarta, or G10, which not only enhance grip but also add aesthetic value. The lock mechanism, which keeps the blade safely in place when open or closed, is another component that requires careful consideration and design.
Advantages of Custom Damascus Folding Knives
Acquiring a custom damascus folding knife is an investment worth making. Here are some of the significant advantages:
- Unique Aesthetics: Every knife has a unique pattern, making each piece one of a kind.
- Exceptional Durability: The layered steel increases strength, making it resistant to shattering and bending.
- Excellent Edge Retention: Damascus steel holds a sharp edge longer than standard steel, reducing the need for frequent sharpening.
- Lightweight: Folding knives are compact and easy to carry, ideal for outdoor activities.
Choosing the Right Custom Damascus Folding Knife
Selecting the right knife can be a daunting task given the vast array of options available. Here are some factors to consider:
1. Purpose
Identify the main use of your knife. Will it be for outdoor gear purposes such as camping, hiking, or fishing? Or do you need it for everyday use? Understanding your needs will help narrow down your choices.
2. Handle Material
Handles can be made from various materials, each offering different grips and aesthetics. Common materials include:
- Wood: Offers a classic look and a warm feel.
- Micarta: A synthetic material that is durable and available in numerous colors.
- G10: A glass-reinforced material that is extremely tough and resistant to elements.
3. Blade Design
Consider the blade shape and length. Different designs serve various purposes, from skinning and slicing to general use.
4. Locking Mechanism
There are several types of locking mechanisms, such as liner lock, frame lock, and lockback. Each has its benefits, and choosing the right one is key to ensuring safety during use.