Exploring Die Casting Machine Factories
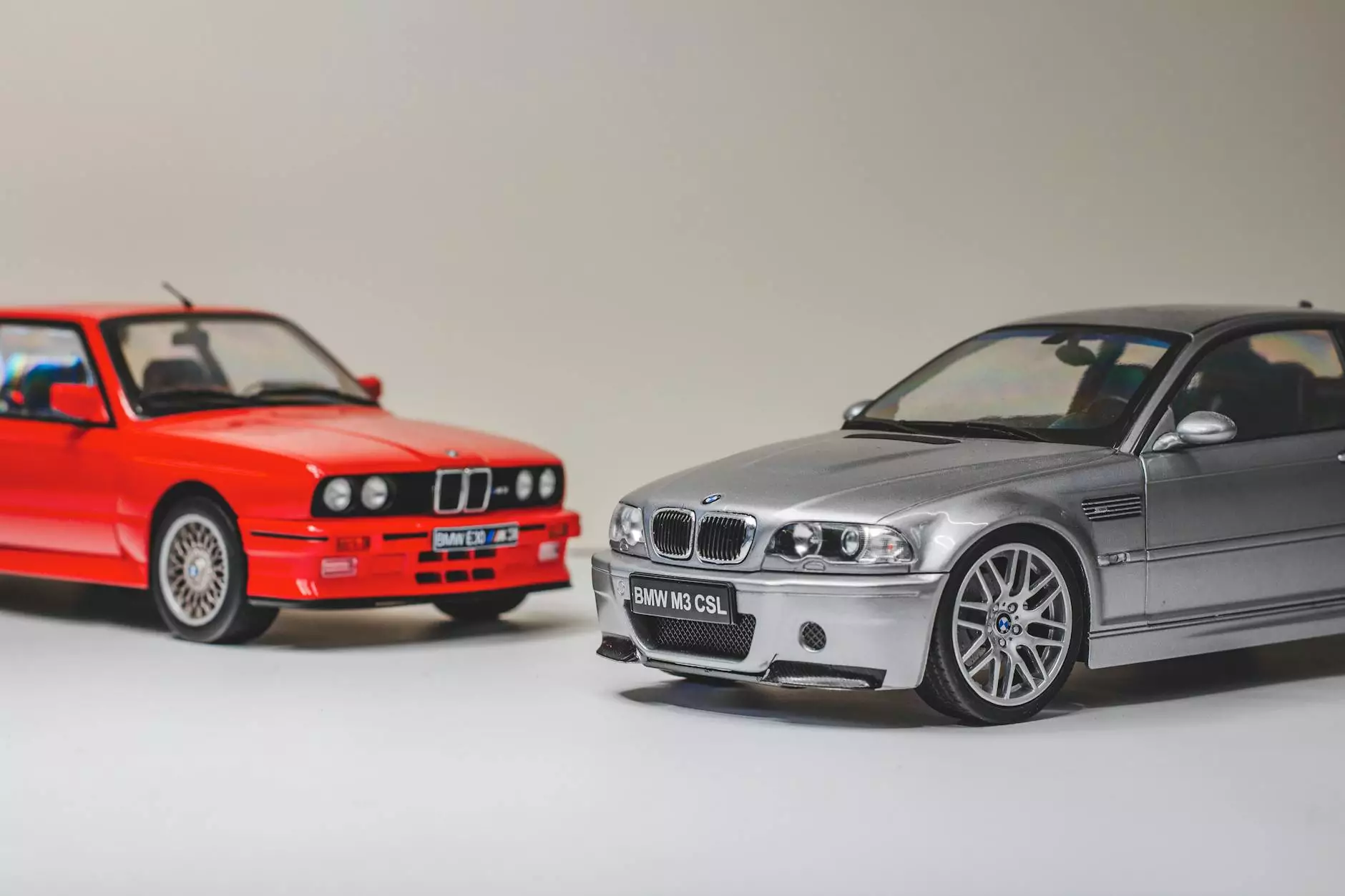
In today's rapidly evolving manufacturing landscape, die casting machine factories stand out as critical players in the production of high-quality metal components. These factories utilize advanced machinery and technology to create intricate parts that are essential across various industries, including automotive, aerospace, and consumer goods. This article delves deeply into the operations, advantages, and future of die casting machine factories, providing an in-depth perspective for enthusiasts and professionals alike.
Understanding Die Casting
Die casting is a manufacturing process that involves forcing molten metal under high pressure into a mold cavity. This method lends itself to the production of complex shapes with excellent dimensional accuracy and smooth surfaces. The die casting process can be categorized into two primary types:
- Hot Chamber Die Casting: Suitable for metals with low melting points, this method maintains the molten metal in the chamber, which allows for faster production cycles.
- Cold Chamber Die Casting: Typically used for metals with high melting points, this method requires the molten metal to be poured into the chamber before injection, resulting in slower production rates but greater versatility.
The Role of Die Casting Machine Factories
Factories dedicated to die casting play a pivotal role in the manufacturing supply chain. They are equipped with sophisticated machines and technology that handle various metal alloys, including aluminum, magnesium, and zinc. Understanding the core operations of these factories is essential.
1. Equipment and Technology
The backbone of any die casting machine factory is its equipment. This includes:
- Die Casting Machines: These machines vary in size and output capability and are crucial for producing high-quality parts.
- Robotic Automation: Increasingly employed for quality control and enhanced precision, robotics streamline the production process.
- Melting Furnaces: Essential for preparing metal alloys for casting.
2. Process Flow in Die Casting
The die casting process typically involves several key stages:
- Preparation: The mold is cleaned and prepared for the injection of molten metal.
- Melting: Metal alloys are melted in furnaces, ensuring the right temperatures for effective casting.
- Injection: Molten metal is injected into the mold under high pressure.
- Cooling: The metal is allowed to cool and solidify, forming the desired shape.
- Finishing: Components are removed from molds and undergo finishing processes like machining and surface treatment.
Benefits of Die Casting
Die casting offers numerous advantages that make it a preferred choice for many manufacturers:
- High Precision: Parts produced via die casting feature tighter tolerances and minimized machining requirements.
- Superior Surface Finish: The process yields a smoother surface compared to other methods, often reducing the need for extensive finishing.
- Cost-Effective for Large Volumes: Once the initial investment in tooling is covered, die casting becomes increasingly economical at scale.
Applications of Die Casting
The versatility of die casting drives its use across various industries. Common applications include:
- Automotive Parts: Components such as engine blocks, transmission cases, and brackets.
- Aerospace Components: Lightweight, robust parts required in aircraft design.
- Consumer Electronics: Housings and structural components for electronic devices.
- Industrial Equipment: Various components in machinery and tools.
The Future of Die Casting Machine Factories
The future of die casting machine factories is bright, driven by advancements in technology and an increased focus on sustainability. Key trends include:
Automation and Industry 4.0
The integration of smart technologies and automation is transforming die casting factories. With Industry 4.0, factories are becoming more efficient, enabling real-time data analysis and maintenance, reducing downtime, and optimizing supply chains.
Focus on Sustainability
As global demand for environmentally friendly manufacturing practices grows, die casting factories are responding by:
- Implementing recycling programs for scrap metals.
- Utilizing energy-efficient melting and processing technologies.
- Reducing waste through improved process control.
Conclusion
In summary, die casting machine factories are vital to modern metal fabrication, offering unparalleled precision, efficiency, and versatility. Their ability to produce intricate components for various applications positions them as central players in multiple industries. With ongoing advancements in technology and a shift towards sustainable practices, the die casting industry is poised for significant growth and innovation in the coming years. Understanding the intricacies of these factories not only underscores their importance but also highlights the exciting opportunities that lie ahead in the manufacturing landscape.
Explore More
For businesses seeking reliable partnerships within the realm of die casting, DeepMould.net stands out as a leading provider. Their commitment to excellence, advanced technology, and expertise in metal fabrication make them a top choice for your manufacturing needs. Explore their services and discover how they can help you succeed in your projects.