The Premier Precision Molding Company: Excellence in Metal Fabrication
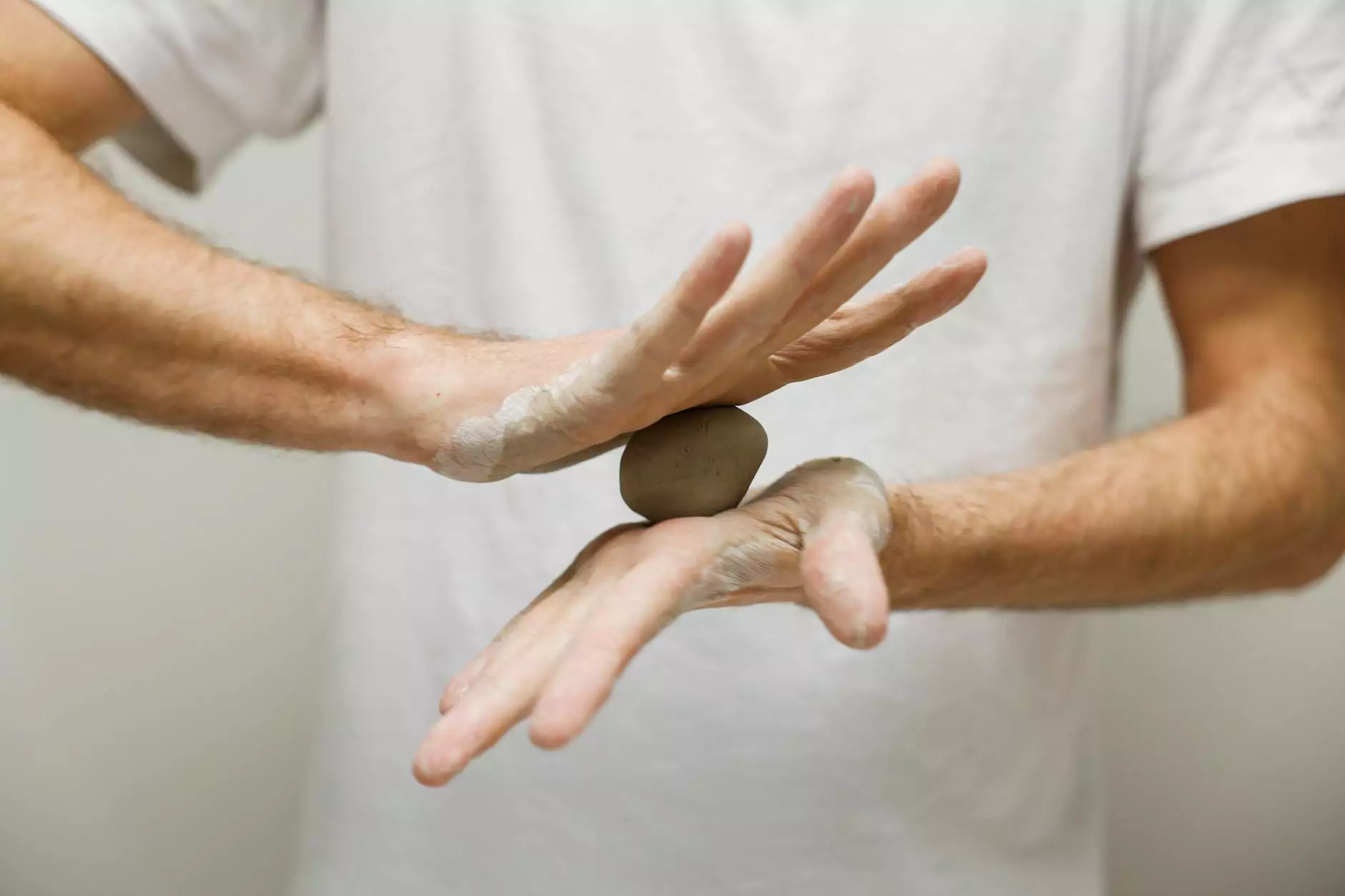
In today's competitive market, a precision molding company plays a crucial role in the production of high-quality components and products. Businesses across various sectors rely heavily on the expertise of metal fabricators to meet their manufacturing needs. This article delves into the significance of precision molding and how it impacts the manufacturing landscape, particularly for Deep Mould, a leading player in the industry.
Understanding Precision Molding
Precision molding is a manufacturing process that involves shaping materials with exceptional accuracy and detail. This technique is essential for creating components that meet stringent tolerances and specifications. The process is widely used in industries such as automotive, aerospace, electronics, and consumer products due to its efficiency and ability to produce complex shapes.
Key Benefits of Precision Molding
- High Precision: Ensures that each component meets exact specifications.
- Cost-Effective: Reduces material waste and lowers production costs.
- Versatile Materials: Compatible with a wide variety of materials including metals, plastics, and composites.
- Rapid Production: Speeds up the manufacturing process, allowing for quicker turnaround times.
- Consistent Quality: Maintains a high standard of quality across all produced items.
The Role of Metal Fabricators in Precision Molding
Metal fabricators are integral to the success of a precision molding company. They possess the technical expertise and machinery needed to manipulate metal into precise shapes. Here’s a breakdown of how metal fabricators contribute to high-quality molding processes:
1. Advanced Technology and Equipment
A leading precision molding company utilizes cutting-edge technology such as CNC machining, laser cutting, and 3D printing. These tools allow metal fabricators to achieve intricate designs and maintain exacting standards, which are essential for industries that rely on precision components.
2. Skilled Workforce
The backbone of any successful precision molding operation is its workforce. Skilled technicians and engineers bring years of experience to the table, ensuring that every project is executed flawlessly. Continuous training and development are vital for staff, keeping them abreast of the latest techniques and safety protocols.
3. Material Selection
Choosing the right materials is vital for any precision molding company. Metal fabricators work closely with clients to understand their requirements, recommending materials that provide the best durability, strength, and cost-effectiveness. Common materials include:
- Aluminum: Lightweight and corrosion-resistant.
- Steel: Known for its strength and versatility.
- Copper: Excellent for electrical applications.
- Stainless Steel: Offers resistance to corrosion and staining.
Precision Molding Techniques
Various techniques are employed in the process of precision molding. Understanding these methods helps businesses choose the right approach for their specific needs.
Injection Molding
Injection molding is one of the most common methods used in precision molding. It involves injecting molten material into a mold, where it cools and solidifies into the desired shape. This method is particularly effective for producing high volumes of identical parts with intricate geometries. Its applications range from automotive parts to medical devices.
Compression Molding
Compression molding is another widely used technique that entails placing a preheated material into a mold cavity and applying pressure to shape it. This method is ideal for larger components and is commonly used in applications such as rubber products and composite materials.
Extrusion Molding
In extrusion molding, material is heated and forced through a shaped die to create continuous lengths of product. This method is efficient for producing parts that require uniform cross-sections, such as tubing, sheets, and profiles.
Quality Control in Precision Molding
Quality control is paramount for a precision molding company. Rigorous testing and inspection protocols ensure that every component meets the specified standards. This includes:
- Dimensional Inspection: Verifying that parts meet precise measurements.
- Visual Inspection: Checking for surface defects or imperfections.
- Performance Testing: Ensuring components function as intended under various conditions.
Applications of Precision Molding
The versatility of precision molding allows it to be utilized in a diverse range of industries. Here are some prominent applications:
Automotive Industry
The automotive sector heavily relies on precision-molded components for everything from engine parts to interior fittings. These components are crucial for enhancing vehicle performance, safety, and aesthetic appeal.
Aerospace Industry
In the aerospace industry, precision molding ensures the production of lightweight yet robust components that meet the stringent regulations of aviation. Precision parts are key in enhancing fuel efficiency and safety of aircraft.
Medical Devices
The medical field requires precision molding for producing critical components in devices such as syringes, surgical instruments, and diagnostic tools. The reliability of these components can have a direct impact on patient care and outcomes.
Consumer Electronics
Consumer electronics depend on precision-molded parts for casings, connectors, and internal components. The growing demand for advanced technology necessitates high-quality precision molding that adheres to the latest standards.
Choosing the Right Precision Molding Company
Selecting the right precision molding company is crucial for ensuring project success. Here are several factors to consider when making your choice:
- Experience: Look for a company with a proven track record in the industry.
- Technology: Ensure they use advanced machinery and technology to meet your requirements.
- Quality Assurance: Investigate their quality control processes to guarantee high standards.
- Customer Support: Choose a company that offers outstanding customer service and communication.
- Reviews and Testimonials: Research feedback from previous clients to gain insight into their reliability and performance.
Conclusion
A precision molding company like Deep Mould is invaluable in today’s manufacturing landscape. By understanding and utilizing advanced techniques, they produce high-quality metal components that meet diverse industry needs. In an era where precision and quality cannot be compromised, partnering with a skilled metal fabricator ensures that your projects are successful and your business thrives.
With constant innovations and improvements in molding technologies, businesses should keep an eye on evolving practices and trends within the industry. The future of manufacturing lies in precision, and with trusted partners, success is within reach.